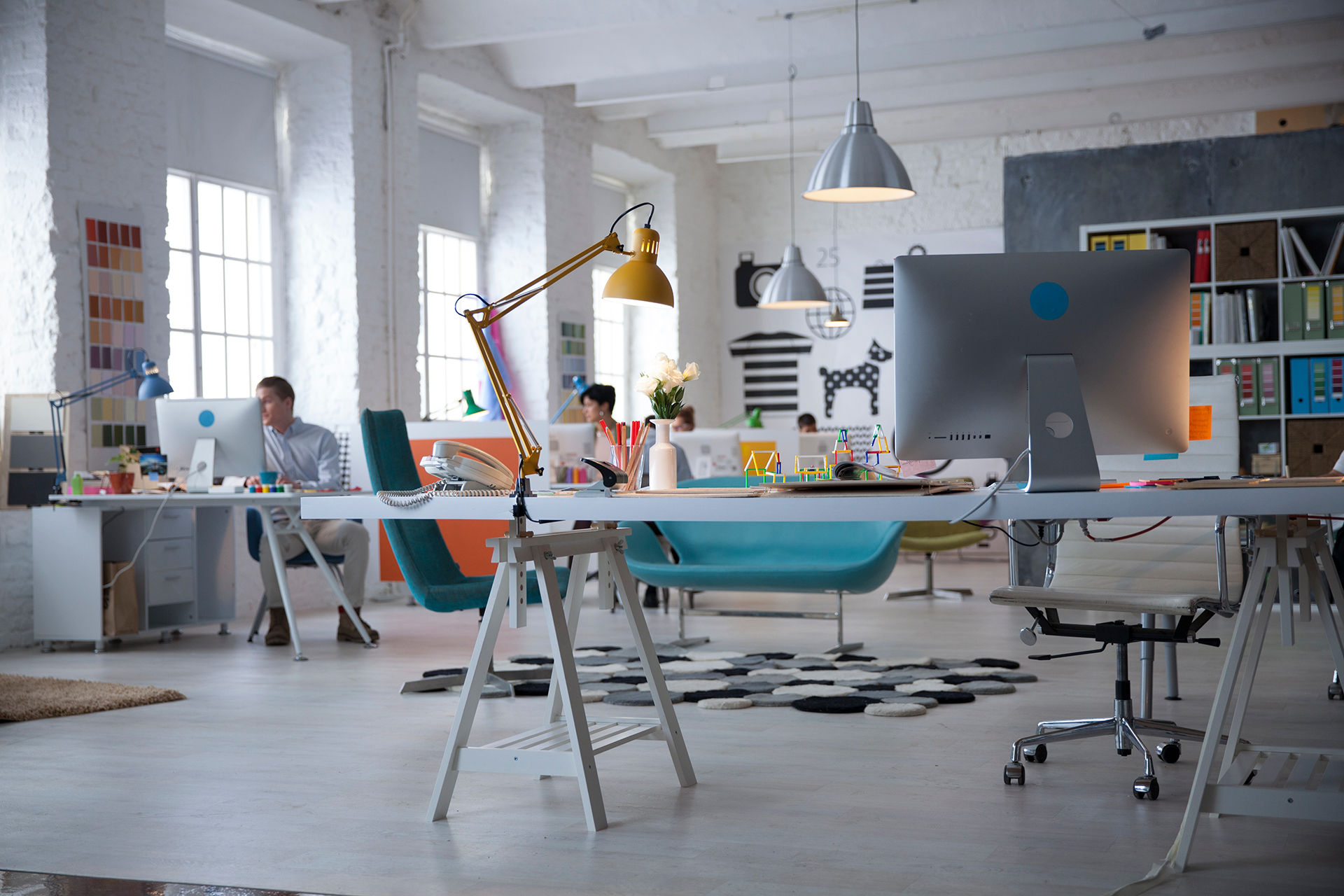
Chariot GRH
Histoire d'une invention
Brevets - GRH
GPG -PPG & Timons
Brevets :
Le 30 mai 1996 , une demande de Brevet Français par Valeo Management Services "Propriété Industrielle "de Créteil 94004 .
Le 4 juin 1996 , nous remplissons une demande de " Déclaration d'Invention de Service " en co-auteurs
- Problème posé
Concevoir un train de Chariots à encombrement axial réduit
- Exposé de la solution
Ensemble de manutention comportant au moins quatre chariots rectangulaire comprenant chacun des roues , un élément de liaison avant et un élément de liaison arrière , et au moins un Timon comportant des organes de liaison adaptés à être reliés à des éléments de liaison , caractérisé en ce que le Timon est adapté à être relié simultanément aux éléments de liaison des quatre chariots lorsque le chariots sont groupés par paires et que les paires sont disposés es se succédant d'avant en arrière , le timon comportant des moyens pour maintenir une distance fixe entre les éléments de liaison des chariots de chaque paire , l'ensemble comportant des moyens pour rendre chaque paire mobile par rapport à l'autre autour d'un axe de rotation vertical unique.
Ces trois brevets sont devenus Européens en date du 13 mars 1997
désignés dans 10 États :
-Autriche , Belgique , Allemagne , Espagne , France , Grande-Bretagne , Italie ,Nederland, Portugal , Suède
GRH :
Le 24 juin 1996 , un " Protocole d'Accord " de quatre pages entre les deux Sociétés est dressé .
Le 25 juin 1996 , nous partons chez notre Fournisseur de la Côte d'Or , de Chariots , Coiffes , Timons pour réaliser les derniers essais et pour valider ceux-ci .
En cours de route nous parlions de donner un nom à ce Chariot tant espéré ,Monsieur Christian Hanquez a eu une formidable idée que nous avons adopté sur le champ.
Si nous l'appelions :
GREAT ROLLER HIGT-TECH
en prenant la première lettre nous pourrions l'appeler:
GRH
se sont nos initiales
G = Godin
R= Ray
H = Hanquez
Nous décidons de faire graver sur le futur moule d'injection du Chariot les trois lettres : GRH
Le 18 Juillet 1996 nous annoncions la naissance et le baptême de notre Chariot ( voir acte ci-dessous)
Nous établissons un "Cahier des Charges " du Chariot GRH :
1- But
Assurer le conditionnement (Bac) des produits Valeo dans un concept global de Logistique transport navette
2-Définition du Chariot
- Format 600 X 400 ( type Gala/Odette )
- Plateau pouvant recevoir tous les bacs de divers fabricants Européens
300 X 200 Gerbable
400 X 600 Gerbable Emboitable
600 X 400 Pliant
- 2 Roulette fixes - 2 roulettes mobiles ( qui doivent être changées par rapport aux essais effectués)
- Vitesse limitée à 5 Kms /heure
- Système de verrouillage intégré dans les deux dimensions : longueur & largeur afin de solidariser deux ensembles Chariot/Bac et/ou de 4 ensembles Chariot/Bac.
- Attelage des ensembles Chariot/Bac les uns derrière les autres ( Tarin tracté)
- Gerbage à vide des Chariots (empreintes roulettes)
- Préhension des ensembles Chariot/Bac par trans-pal , Fenwick, Clark , etc...
- Marquage - identification des Chariots
- Coloris Valeo
- Charge/Chariot : 350 kgs maxi
- Sanglage des ensembles Chariot/Bac
- Création de deux formats de Coiffe :
800 X 600
1200 X 800
assurant le Gerbage 1 sur 1 en transport ou stockage
assurant le maintien des charges
Godin-Ray-Hanquez
Pourquoi développer un nouveau Chariot de manutention au format 600 X 400 : note datée du 27-01-1997
Ce concept de Chariot 600 X 400 a été développé dans un but d'optimisation du flux global du Fournisseur jusqu'au Client.
Ces Chariots peuvent :
-s'utiliser unitairement au poste de travail afin d'obtenir une bonne ergonomie ( avec élévateur pour mise à niveau ou déchargement des bacs en approvisionnement dynamique
- se manipuler unitairement pour approvisionner le poste de travail sans effort , ni moyen de manutention
- s'accrocher entre eux pour constituer un train de 2 à 16 Chariots
- Constituer une unité de manutention pour le transport en Camion
But de ce concept :
Optimisation du flux physique Fournisseurs , Valeo et Clients
- optimiser les transports des pièces dans l'usine par l'utilisation de trains ( transport de 8 unités de manutention à la fois au lieu de 2 avec un car à fourches )
- rendre l'opérateur autonome dans l'approvisionnement de son poste de travail sans perte de temps ni fatigue
- optimiser l'ergonomie au poste de travail notamment pour les pièces lourdes
- réduire l'encombrement et la surface utilisée au poste de travail ( gain de 75% en place au poste de travail par rapport à une unité de manutention 1200 x 1000 )
- supprimer les cars à fourches et moyens de manutention en usine ( sauf réception et expédition) gain sur aspect sécurité , propreté , maintenance et location des moyens)
- supprimer les palettes , cartons , filmage ( gain en propreté de l'usine , suppression des gaspillages liés à la manipulation des cartons )
- standardisation des moyens de transport des pièces
- livraison cyclée des lignes de production ( contrôle de la fonction approvisionnement ,clareté des lignes de production , organisation optimisée)
- réduction de la taille de lot